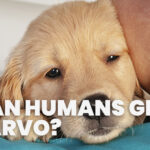
What are the Current Good Manufacturing Practices?
Good Manufacturing Practices Guidelines
Good manufacturing practices guidelines are followed by manufacturers who produce beverages, food, pharmaceuticals, medical devices, etc. Good manufacturing practices are also known as Current Good Manufacturing Practices (cGMP) which is to remind manufacturers that they should be up to date by using the latest systems & technologies to ensure good manufacturing services.
Good Manufacturing Practices are being followed by many companies that manufacture different products in many nations. Also, different regulatory agencies enforce Good Manufacturing Practices regulations in different nations. GMP practices differ from industry to industry & GMP compliance requirements may also vary from nation to nation and industry to industry.
Basic provisions of GMP are to ensure high quality, consistency of manufacturing, effective employee training, proper documentation, and quality assurance testing at various times during the production process.
Good Manufacturing Practices are not prescriptive which means there are numerous ways to meet them. For example, different companies which belong to the same industry & nation can establish different methods to comply with GMP regulations.
So basically, companies will make their own choices based on what is most efficient & effective for them. Companies, to enforce Good Manufacturing Processes, make use of a quality management system (QMS).
Key principles involved in cGMP:
- Maintain clean & hygienic manufacturing area
- Prevent cross-contamination by controlling environmental conditions
- Clearly define & control the manufacturing process
- Ensure consistency & compliance by validating critical processes
- Evaluate changes to manufacturing processes
- Ensure instructions & procedures are written in an unambiguous language that will be easy to understand
- Properly train operators who are in the manufacturing facility to carry out procedures
- Record & document all instructions & procedures that are followed during the manufacturing process
- Record & document that the item manufactured was in the quality as expected
- Maintain records of manufacturing & distribution so that even a full history of a manufactured batch can be traced
- Logically store those records so that it is easy to access
- Make use of distribution procedures & techniques that will reduce the risk involved in the quality of products
- Create a proper recall system to retrieve batches from supply or consumers when necessary
- In case of defective products, investigate product complaints, quality defects and take proper measures
To follow CGMP guidelines, companies should establish strong quality management systems, implement robust operating procedures, use good quality raw materials, screen and investigate product quality deviations and maintain reliable testing laboratories. If cGMP guidelines are followed, companies can avoid most of the common causes of quality failure.
Importance of Current Good Manufacturing Practice (cGMP) in Pharmaceuticals
The quality of pharmaceuticals is regulated by The Food and Drug Administration (FDA). The main regulatory standard to ensure pharmaceutical quality is the CMPG regulation for pharmaceuticals.
To conform to the guidelines that are suggested by agencies that control both the authorization & licensing of the manufacture & sale of cosmetics, food & beverage, dietary supplements, pharmaceuticals, and medical devices, it is imperative to practice Good Manufacturing Practices. To ensure the quality of drug products, FDA carefully monitors the drug manufacturer’s compliance with cGMP regulations.
The cGMP regulations for drugs have minimal requirements for the facilities, methods, and controls used in the manufacturing, processing, and packaging of the drug product. These regulations require that processors, manufacturers, and packagers of drugs, food, medical devices, etc., should take proactive steps to make sure their products are pure, safe, and effective.
The main purpose of GMP is basically to prevent harm to the end-user and also ensure that the product is free from any contamination. cGMP is important because consumers cannot detect whether a drug product is safe and that is why cGMPs require testing to ensure its quality.
FAQs
1. What are the 5 main components of good manufacturing practice?
The 5 Ps of Good Manufacturing Practice is people, premises, products, processes, and procedures.
2. What are good manufacturing practices examples?
Examples of Good Manufacturing Practices may include maintaining a clean manufacturing area, maintain controlled environmental conditions, clearly defined &controlled manufacturing processes, validate processes, record instructions & procedures, train operators, etc.
3. What is the GMP standard?
GMP ensures that products are produced and controlled adhering to the quality standards. All aspects of production, premises, materials, training, hygiene, etc will be entirely covered.